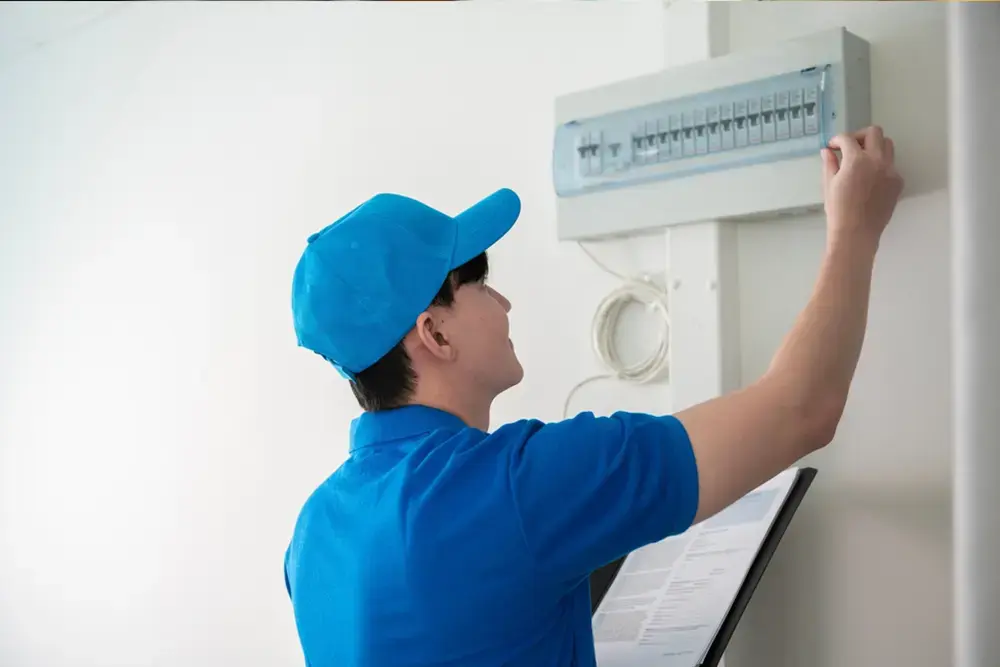
Electrical safety is a major concern in workplaces and homes across Australia. Electrical equipment needs to go through the process of testing and tagging to make sure they are safe to use, which also reduces the risk of electric shock and accidental fires. If you own a business or you are a homeowner, this blog will help you understand the test and tag standards in Australia. So you can maintain compliance, increase safety, and adhere to safety regulations.
What are Test and Tag Standards? (AS/NZS 3760:2022)
AS/NZS 3760:2022
The AS/NZS 3760 2022 is the Australian and New Zealand standard that helps in setting the guidelines for testing and tagging various electrical equipment. This standard includes:
- The procedure for properly inspecting and testing various electrical appliances.
- The frequency of testing for each type of equipment and also for various work environments
- Who can conduct testing
- Documentation and compliance guidelines
The AS/NZS 3760:2022 standard helps in making sure that all businesses maintain electrical safety standards to prevent accidents and equipment failures.
Core Components of Test and Tag Standards
The test and tag process has 3 steps in total
- Visual Inspection: First step is checking for any visible signs of damage, wear & tear, or faults in the electrical equipment.
- Electrical Testing: Next step involves using special equipment to test insulation resistance, earth continuity, and polarity in the electrical equipment.
- Tagging: In the final step, the equipment is labeled with a test tag that has details like the date of the test, due date for test, and also the information about the tester.
These steps are in compliance with Australian test and tag regulations and helps in protecting employees and businesses from electrical hazards.
Regulatory Considerations in Australia
Businesses and other commercial spaces in Australia must comply with workplace health and safety (WHS) laws that require all electrical equipment to be safe for use. This includes:
- Regular testing of electrical equipment as per the AS/NZS 3760:2022 standards
- Maintaining proper records of all testing and tagging processes
- Making sure that only qualified personnel perform the tests
- Addressing the faults in electrical equipment immediately to prevent hazards
Failure to comply with test and tag regulations may lead to legal risks, workplace accidents, or insurance claim issues.
Equipment Assessment: What Needs Testing?
Electrical Equipment That Requires Testing:
Electrical appliances that are used in workplaces or public spaces must be tested. These include:
- Power tools
- Office equipment (computers, printers, etc.)
- Kitchen appliances (microwaves, kettles, etc.)
- Portable RCDs (Residual Current Devices)
- Industrial equipment
Equipment Exempt from Testing:
Some electrical items do not need routine tests and tags, these equipment include:
- Fixed or hard-wired appliances (e.g., built-in air conditioners, wired-in stoves)
- Equipment that works below 50V (such as low-voltage LED lights)
- Single-use or disposable electrical items
How often should you test and tag?
The frequency of testing and tagging depends on the type of equipment and the place in which it is used. The AS/NZS 3760:2022 test tag standards mention the different testing intervals:
- Construction sites: Every 3 months
- Factories and workshops: Every 6 months
- Office spaces and low-risk environments: Every 5 years
- Portable RCDs: Every 6 months
- Hire equipment: Before each hire, then every 3 months
Regular testing allows the electrical equipment to be in safe working condition and prevents accidental electrical issues.
Types of Electrical Equipment
In electrical equipment, there are different categories based on the usage and risk level:
- Category I Electrical Equipment (Earthed Appliances): These equipment have a protective earth connection. They include kettles, microwaves, power tools, etc.
- Category II Electrical Equipment (Double Insulated Appliances): Equipment that do not rely on an earth connection and have double insulation for safety fall under the 2nd category. These include: hair dryers, electric drills, etc.
- Residual Current Devices (RCDs): RCD devices are very helpful because they can detect the leakage of currents and help people in commercial and residential spaces prevent electric shocks.
These electrical equipment categories help businesses know about the necessary tests and safety measures for the various equipment they use.
What Tests Should Be Done on Appliances and Equipment?
The AS3760 testing and tagging of equipment have many electrical tests, like:
- Visual Inspection: Identifying any physical damage on the electrical equipment, and also checking if there are any exposed wires or even signs of overheating.
- Earth Continuity Test: This test helps in making sure that there is proper grounding of earthed appliances (category 1 equipment).
- Insulation Resistance Test: Insulation resistance test helps testers to check if the insulation has not been damaged to prevent electric shock.
- Polarity Test: To make sure there is correct wiring in extension cords and power boards.
- RCD Testing: The AS NZA 3760 RCD testing is for checking the trip of Residual Current Devices (RCDs) at the required current levels.
Each test helps the tester to confirm that an electrical appliance meets all the safety standards and can function properly and safely.
Who Can Do the Testing?
The test and tag procedure must be performed by a competent person, according to the standards. This means only those who have completed relevant training to test and tag electrical equipment can conduct the test. This can be:
- A qualified electrician
- A certified test and tag technician
- A person who has undergone training under the AS/NZS 3760 standards
By hiring a professional for the test and tag process in your space, you can make sure that all tests are conducted properly and as per the legal standards.
Documentation for testing and tagging
Maintaining proper records for the AS NZS 3760 test and tag process helps businesses maintain compliance with regulations. Here are the documents that are needed for the test and tag:
- The appliance ID
- The date of the test
- The name of the tester
- The test results (pass/fail)
- The next due date for testing
These records should be stored safely so that they are available for next audits, inspections, or insurance claims.
Conclusion
In conclusion, understanding and following the test and tag Australian standards AS/NZS 3760:2022, is important for workplace safety and compliance with regulations in Australia. By regularly testing your electrical equipment, you can help prevent electrical accidents, reduce downtime, and make sure that your business meets legal standards.